What is a Linear Actuator?
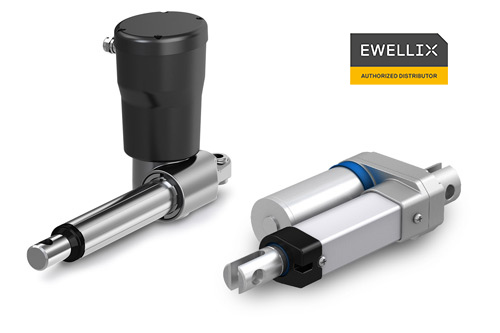
A linear actuator which provides a push/pull force is often called an electric actuator. These actuators are telescopic and use a push tube using either a lead screw, ball screw or roller screw. They are complete with a basic electric motor (typically 24VDC or 12VDC, but AC versions are also available) and gear to provide a fixed choice of speed and force. They typically have strokes in the 50mm – 700mm range, with forces from 50N to 500kN (from high performance versions). Electric actuators are used where the duty cycle is typically in the 10-25% range.
High Performance linear actuators are also based on a telescopic push/pull capability. However, they are often supplied without motors so that these can be chosen to best match the particular application. Servo motors are also common (a servo linear actuator), which enables external control of the movement profile, speed, torque, etc. High Performance linear actuators are available complete with motors offering forces up to 500kN. There is increasing interest in such actuators to replace hydraulic actuators, for the control and environmental advantages that they offer.
Positioning linear actuators are used to provide linear positioning of loads, often large. Many different versions are available, providing differing performance characteristics. These actuators typically offer repeatability positioning from a few microns to 100 microns, with loads from a few grams to 1000s kgs. Construction is often an aluminium extrusion, to which linear guide rails are fitted, with drive coming from either a belt or ball screw. Belt driven actuators are very useful for long stroke applications, where strokes in excess of 10m are possible. A variety of motors are fitted according to the application.
Servo linear actuators are actuators, either push/pull telescopic or positioning, which are combined with a servo motor. A servo motor allows the motor to exchange information with, and be controlled by, an external control system, eg a PLC. This allows for varying speed, stroke, torque control, etc. Servo actuators are also used when 100% duty cycle is required.
Pneumatic linear actuators are also widely used. These tend to be simple push/pull applications. They have the advantage of potentially higher speeds and low cost. However, there is a significant move away from pneumatic actuators to electric and servo actuators, due to the control and environmental benefits offered by these systems.