Selecting the right linear actuator
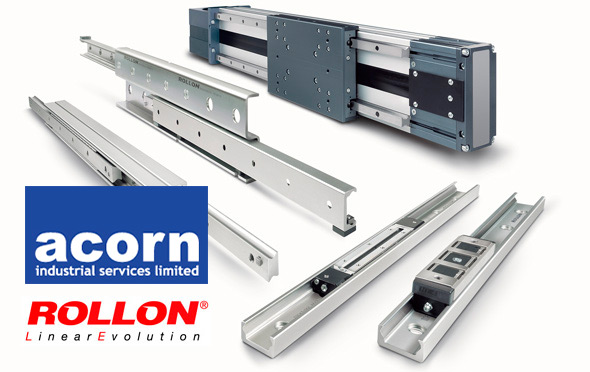
Rollon has designed this nine point guide to help customers choose the right actuator using the packaging industry as a sample field of application. Here are nine tips that take the main variables into consideration to guarantee performance and suitable costs.
- Precision and accuracy. First, assess the levels of precision, accuracy and repeatability required for the application. As a rule of thumb, end-of-line packaging machinery usually requires maximum positioning repeatability of ±0.05 mm. This level of precision is considered excellent performance in this sector, and it can be achieved with belt driven or rack and pinion actuators, which guarantee repeatable, reliable movement that is precise. A linear encoder can be used for an even higher level of positioning precision.
- Load capacity. The load capacity of an actuator depends on the structure of the profiles being used. Many actuators look alike, but only some are designed to manage heavy loads at high speeds. This is why it is a good idea to evaluate parameters like thrust, dynamic loads and bending moment when looking for the right actuator for packaging lines for heavy loads.
- Space and stroke length. There is a difference between using a 3-axis end of line system with its own aerial structure rather than individual units integrated into the machine. These two applications require different amounts of space, and the second option could require a custom-designed solution. Stroke length can also influence the choice: for example, for strokes longer than 8 m, rack and pinion actuators become indispensable because they can prevent imprecision caused by the elasticity of the toothed belt.
- Work cycles. For intense, heavy work cycles and constant use, maintenance and lubrication need to be done regularly according to a specific maintenance plan.
- Operating environment. In work environments where dirt can have a negative impact on the quality of movement, it is necessary to use pressurized linear motion units that can function correctly and guarantee performance even in particularly dirty environments.
- Spatial orientation. Before choosing an actuator, it is necessary to know the spatial orientation that it will have, and also the orientations of the loads and forces, regardless of whether the machine is a multi-axis system or made up of individual units. Also, assembly options need to be considered (vertical or horizontal?) in addition to the connections between actuators in multi-axis configurations. It is extremely important for supplies requiring brackets and plates to guarantee rigid connections between actuators. Improperly connected actuators could, cause problems such as misalignment, vibrations, reduced precision, or other issues.
- Speed and acceleration. To obtain performance levels such as resistance to high loads at a speed of 5 m/s and accelerations of up to 50 m/s2, it is a good idea to use a direct rigid coupling between the pulley and the geared motor. Caged recirculating ball bearing rails, which can reduce friction between the ball bearings inside the runner blocks, can be used to reach the highest standards.
- Structural characteristics of the actuator. Most actuators are made of anodized extruded aluminum so that they can be strong but lightweight. The profile structure is fundamental: a greater thickness and correct geometry make it possible to obtain higher rigidity and inertia. The sliding system is also crucial: rails with preloaded recirculating ball bearings improve the accuracy, repeatability and rigidity of the system. Steel roller rails, which can also be coated in plastic, are an excellent solution for managing misalignment and for use in dirty environments.
- Pairing reducer and motor. The choice of the reducer, both for belt driven and rack and pinion systems, plays an important part in maintaining system precision and improving the ratio of inertia between the motor and the mass being moved. For this reason, the best (choice would be a linear axis with the reducer already installed and the correct dimensioning of the motor.
Rollon has added new models to its actuator range through the acquisition of Tecno Center. This Turin-based company brought advanced, more complex products that are comple-mentary to Rollon's lines for the white goods, automotive and machine tools industries, and the merger has created one of the most competitive selections of actuators in the world.
Need further information? Our linear experts can ensure you get the right actuator for your application.