New bearing solution leads to extra cake
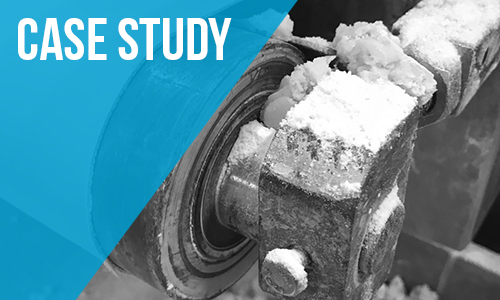
After a series of bearing failures and repeated downtime, a leading manufacturer of baked goods contacted Acorn Industrial Services to request a site visit. Following a preliminary meeting, ACORN undertook a process line mapping exercise to assess where improvements could be made to increase the uptime of the plant and reduce bearing failure.
The plant’s site manager believed that many bearings on the line were repeatedly failing as a result of contamination. The average lifespan of these bearings was just 10 weeks, with downtime and maintenance man-hours stacking up.
ACORN’s Bearing and Maintenance Product Manager, Andrew Fletcher, visited the site to investigate the cause of the repeated bearing failures and to identify areas for improvement.
The area of most concern was their fondant machines. The machines were fitted with deep groove ball bearings equipped with 2RS seals. Although these machines were free from external contaminants, the bearings were covered in icing and flour, suggesting that they were becoming heavily contaminated. Meanwhile, frequent washdowns were causing the bearings to corrode. It quickly became apparent that none of the bearings in the plant were stainless steel. Stainless steel is typically the chosen material for a food production environment thanks to its high levels of corrosion resistance.
The situation was similar in the other areas of the production line, with bearings suffering from high levels of contamination without adequate protection, as well as being subject to corrosion. Without intervention, it’s likely that these bearings would continue to fail again and again, causing unnecessary downtime and loss of production for the plant.
After a full assessment of the process line, Andy put together a report documenting the issues with the current setup, along with suggested improvements to increase uptime on the production line.
The first improvement that Andy was able to suggest was to upgrade the bearings to stainless steel. This would help to reduce failures caused by corrosion, extending the lifespan of the bearings by up to 75%.
The sealing on the bearings could also be improved to guard against water and particle contamination. For this, Andy suggested several solutions and the possible outcomes for each. Presented with this data, the customer was able to clearly see the benefits of changing to an improved solution, eventually choosing NSK’s deep groove ball bearings, fitted with a DDU sealing solution. Upgrading to these contact sealed bearings could increase the bearing lifespan by up to 50%.
The life expectancy of the bearings could be further increased by opting to add Nilos rings to the bearings. These rings would help to deflect the initial washdown and the majority of particle contaminants, with the DDU seal acting as a second-line defence.
Andy estimated that making the suggested changes had the potential to increase the bearings’ service life by over 300%, extending the lifespan from just 10 weeks to up to 34 weeks. By providing a detailed report to the customer, Andy was able to demonstrate Total Cost of Ownership (TCO). The savings in maintenance and repair, along with the reduction in downtime and loss of production would more than negate the cost of upgrading the bearings.
The ACORN: EXTRA service prioritises Total Cost of Ownership, working hand-in-hand with businesses to solve their application challenges. This unique service is available to all businesses across every industry, from food and beverage to processing and packaging. Businesses are able to gain insider access to some of the industry’s leading experts. These experts will work to understand the unique challenges of the business, and then work closely with site staff to identify the right solutions.
From production line mapping and application reviews to failure analysis and product training, the ACORN: EXTRA service will appeal to every business.