CASE STUDY: Cost and Environmental Savings Through Bearing Refurbishment for Paper Manufacturer
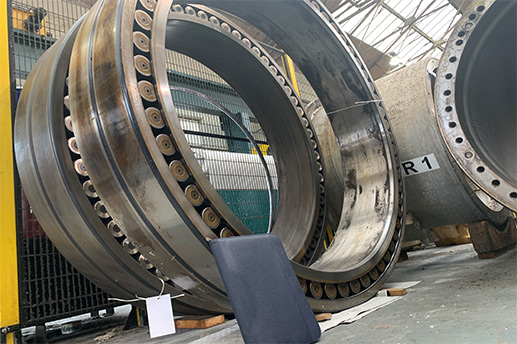
A large paper manufacturing plant was facing significant operational challenges due to the long lead times and high costs associated with replacing two large FAG 48/1400-B-K30-MB-C3 spherical roller bearings. These bearings are critical components in their manufacturing process, responsible for keeping key machinery operational and ensuring smooth production. Any downtime caused by bearing failure or delays in replacement could lead to costly disruptions in production and lost revenue.
The cost of replacing each spherical roller bearing was £69,950, a substantial investment for the plant. Additionally, sourcing new bearings involved long lead times due to supply chain delays, which posed a significant risk of extended downtime. This situation was further complicated by the environmental impact of producing and transporting new bearings, which contributed a considerable amount of CO2 emissions.
The manufacturer was under pressure to find a more cost-effective and sustainable solution while ensuring that the production line remained operational without significant delays.
To address the challenges, Andy Fletcher, the Bearing Product Manager, teamed up with Phil McLaughlin, the Regional Sales Manager, to explore alternatives. They identified the option of refurbishing the existing bearings rather than replacing them with new ones.
The two damaged bearings were sent for refurbishment at a cost of £42,300 each, significantly lower than the price of purchasing new bearings. By opting for refurbishment, the company achieved a direct cost saving of £27,650 per bearing, resulting in a total savings of £55,300 for the two bearings.
Not only this, but the environmental impact of refurbishing the bearings was significant. Refurbishing the bearings saved the customer 10,358.8kg of CO2, the equivalent of the emissions generated by 5 flights between London and Sydney. This significantly contributed to the company’s efforts to reduce its carbon footprint and align with global environmental standards.
Andy Fletcher's and Phil McLaughlin's collaboration exemplified how innovative thinking and teamwork can deliver economic and environmental benefits to manufacturing operations.
This case serves as an excellent example of how businesses can balance cost-efficiency with sustainability in their operations, benefiting both the company’s bottom line and the environment.
This case study has been selected as a finalist in the Sustainable Engineering category at the AEMT Awards 2024!