CASE STUDY: Chain Solution for Cereal Manufacturer
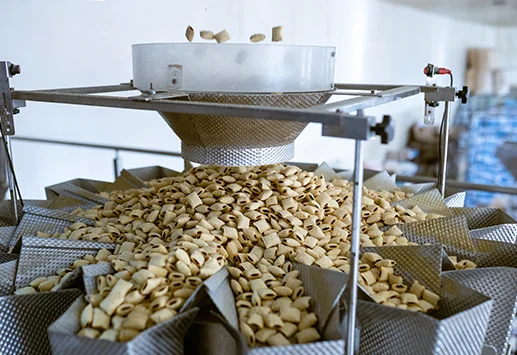
During a routine visit to a national food manufacturer on the Wirral, Business Development Manager, Lee Dobson was approached by an Engineering Manager regarding a critical issue affecting production. The bucket elevator system, essential for cereal manufacturing, was experiencing excessive chain wear. The original manufacturer has gone into administration, leaving the customer without a direct replacement source.
Four well-established companies had attempted to address the issue but failed to provide a viable long-term solution. Their recommendations suggested replacing the entire bucket elevator system at a staggering cost of £220,000.
Actions & Solutions
Recognising the urgency of the situation, Lee developed a two-stage solution to ensure continued production while minimising costs.
For the short-term fix, the chain had reached maximum tension but remained loose within the elevator unit due to excessive pin and bush wear, which has caused 800mm travel to maximum tension. Given that the buckets were fixed on every third outer plate, with the help of the power transmission product manager, Paul Speight, Lee identified and removed a complete bucket assembly with three outer chain links. This adjustment reduced slack, allowing the system to be re-tensioned and resume operations without further disruption.
For the long-term solutions, they aimed to prevent recurring wear issues by sourcing a custom-manufactured chain, designed to the original specifications. This solution ensured seamless integration into the existing system, eliminating the need for an entirely new bucket elevator.
Results
The implemented solution delivered substantial financial and operational benefits. By avoiding the capital expenditure of £220,000 on a new bucket elevator, the customer achieved a direct cost saving of £209,000 with a total solution cost of just £11,000. Additionally, there was no production downtime, ensuring continued revenue generation for the Food Manufacturer. The newly sourced chain also enhanced durability, reducing future maintenance requirements.
Conclusion
Through innovative problem-solving and a deep understanding of the customer's operational needs, we delivered an effective, cost-efficient solution that outperformed previous recommendations. This highlights the value of engineering expertise and strategic sourcing in maintaining critical manufacturing processes while achieving significant cost savings.