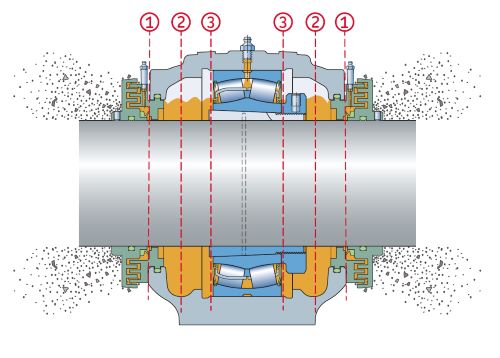
A specialised solution for highly contaminated environments: three barriers protect the bearing from contaminants – leading to extended bearing service life.
The upgraded SKF Three-barrier solution means re-greasing twice a year instead of once a week, saving up to 90% of the time and cost of greasing (up to 99.9% if not purged) and increasing safety for maintenance workers.
Faster mounting and dismounting
Reduced maintenance costs
Wide range of available sizes and accessories
Reduced environmental impact
Longer bearing and mining seal service life
Good low-temperature start-up performance
good corrosion-inhibiting properties
Suitable for medium to high loads
Reduce the risk of failure
Reduce your overall costs
Reduce environmental footprint
Reduce the risk of worker injury
A reliable solution for mounted bearings in punishing operating environments, these housings can help cut maintenance costs, drive reliability, and extend bearing service life for a range of machinery.
SKF SNL/SAF housings are manufactured to world-class quality standards to meet the extreme demands of mining operations. Giving you longer service life, easier mounting, less maintenance, and longer relubrication intervals
Designed for split housings in extremely contaminated and wet applications, these seals help to keep contaminants out of bearing arrangements. Ensuring superior protection, SKF Taconite seals help exclude contaminants and water, reduce greasing intervals and extend bearing service life.
You can also expect improved water ingress prevention even during high-pressure washdowns. The SKF Taconite seals are compatible with new and older housings.
SKF LGGB 2 is a biodegradable, low toxicity, synthetic ester oil-based grease, using a lithium-calcium thickener. Its special formulation makes it most suitable for applications where environmental contamination is a concern. They offer good performance in applications with steel-on-steel spherical plain bearings, ball bearings, and roller bearings.
Typical applications:
In critical production lines, every minute of downtime costs. Contaminated environments and heavy loads in applications prone to misalignment or shaft deflections are daily issues for many industries.
With sealed SKF Explorer spherical roller bearings, you’re equipped to meet these challenges. Pre-lubricated with specially formulated grease and sealed with high-performance contact seals, they can protect the bearing and lubricant from contaminants that might otherwise cause premature bearing failure.
Check out our range of SKF split plumber block housings
Check out our range of SKF housing sealing solutions
Check out our range of SKF greases
Check out our range of SKF Spherical roller bearings
We aim to respond to emails within 24hrs
Mon - Fri: 8am - 6pm
Contact information for our branches and divisions.
Trust ACORN for business services that include expert advice, premium products, and excellent customer support. Your partner for reliable and efficient industrial solutions
ACORN's industry experts offer premium products, expert advice, and excellent customer support. Choose us for reliable and efficient solutions in your industry
ACORN's local branches provide expert advice, quality products, and exceptional service. Visit us for reliable industrial solutions and personalised support near you
ACORN offers reliable international delivery, ensuring top-quality industrial products reach you wherever you are. Trust us for efficient and timely global shipping. Our export team will be happy to answer your questions
It is commonly used in:
By preventing contaminants from entering the bearing, the SKF Three-Barrier Solution reduces the likelihood of premature bearing failure. This enhances the overall reliability of machinery by:
To determine if the SKF Three-Barrier Solution is suitable for your application, consider the following factors: