Which bearings are used for high speed?
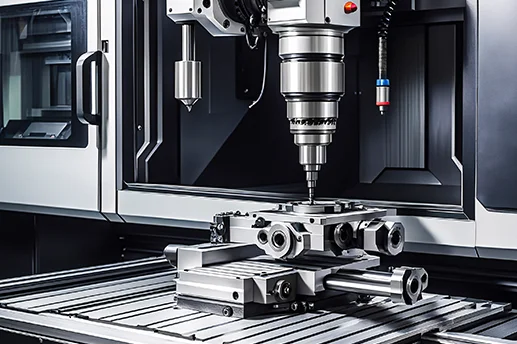
Precision bearings play a vital role in high-performance and high-accuracy applications across many industries. These components are designed to deliver unmatched precision, reliability, and durability, ensuring the seamless operation of machinery in environments where even the slightest differences can lead to significant issues. But which bearings are best suited for high-speed applications? Let’s explore some common types and the factors affecting their speed capabilities.
Super precision ball bearings
Super precision ball bearings are a versatile choice for high-speed applications. They are reliable and can handle both axial and radial loads. Their design eliminates the need to use them in pairs, making them particularly suitable for environments with limited space, where compact and efficient solutions are needed.
Super precision angular contact ball bearings
Super Precision Angular contact ball bearings are engineered for high-speed operations. They can support radial and axial loads simultaneously, making them ideal for applications demanding both speed and stability.
Super precision cylindrical roller bearings
Super Precision Cylindrical roller bearings excel in applications requiring high precision tolerances and superior durability. With optimised cage configurations and high-quality materials available, these bearings ensure consistent performance and an extended service life, even under demanding conditions. Their capacity to handle heavy loads and operate efficiently at high speeds makes them a preferred choice in many industrial settings.
What affects speed?
Several critical factors can influence the speed capabilities of bearings, including:
DmN factor
The DmN factor of a bearing is a calculation that combines the bearing’s pitch diameter (Dm) and its speed (n). It serves as a benchmark for determining the maximum allowable speed of a bearing. Bearings with DmN ratings are better suited for high-speed applications.
Lubrication
Proper lubrication is vital for reducing friction and heat generation in high-speed bearings, especially as approximately 36% of premature bearing failures are due to improper lubrication (SKF, 2022).
- Lubrication oil: Often preferred for high-speed applications due to its superior heat dissipation and reduced drag.
- Grease lubrication: While simpler to apply, grease can limit speed due to its higher viscosity. Bearings designed for grease lubrication often include oil holes to enhance distribution and performance.
Ceramic balls vs standard steel
Ceramic balls are a game-changer for high-speed applications. Compared to steel balls, they are lighter, generate less heat, and reduce centrifugal forces. This allows bearings with ceramic balls to achieve higher speeds and operate more efficiently over time.
Materials and Cage Design
Special materials, such as hybrid ceramics and optimised cage designs, further enhance speed ratings. Advance cage configurations reduce friction and ensure uniform ball spacing, minimising vibrations and wear during high-speed operation.
Choosing the right high-speed bearing
When selecting a bearing for high-speed applications, it’s essential to evaluate the operating conditions, including load type, temperature, lubrication requirements, and the desired speed. Consulting with manufacturers or bearing specialists can help you identify the optimal bearing type and configuration for your specific needs.
High-speed bearings are indispensable in industries ranging from aerospace to robotics. Understanding their characteristics and the factors that influence their performance will help you to make informed decisions and ensure the reliability and efficiency of your equipment. If in doubt, you can talk to our product experts for assistance with selecting to best product for your application.