What is predictive maintenance?
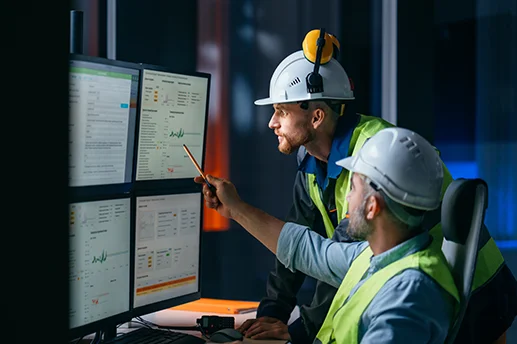
With rising costs and increasing production demands, unplanned downtime is more expensive than ever. Businesses cannot afford unexpected breakdowns, but with a structured maintenance plan, they do not have to. Predictive maintenance helps you stay one step ahead by identifying potential failures before they happen, so you can plan ahead, reduce costs, and keep operations running smoothly.
Definition
Predictive maintenance monitors machine conditions, such as vibration and temperature, to assess equipment health and anticipate when maintenance is needed. By spotting early warning signs, businesses can avoid unexpected failures, schedule servicing at the right time, and extend the life of their machinery.
Why choose predictive maintenance?
The benefits of predictive maintenance go beyond just preventing breakdowns. Here is how it can improve your operations.
Greater equipment reliability
Predictive maintenance improves equipment reliability by using real-time data and analytics to detect issues before they cause breakdowns. Continuous monitoring helps identify early signs of wear or failure, allowing proactive intervention. This reduces unplanned downtime and extends equipment lifespan, improving productivity.
Cost reduction and efficiency gains
Unnecessary maintenance wastes time and resources, while unexpected breakdowns lead to costly repairs. Predictive maintenance ensures servicing happens only when needed, cutting emergency repair costs, reducing downtime, and optimising labour and spare parts usage.
Improved safety and compliance
Faulty equipment can pose serious safety risks. By identifying hazards early, predictive maintenance helps protect your team, ensure compliance with safety regulations, and reduce legal liabilities while fostering a safer work environment.
Smarter, data-driven decisions
With real-time insights from sensors and analytics, businesses can make informed decisions about maintenance priorities. Predictive maintenance allows for smarter resource allocation, ensuring repairs and replacements happen at the right time and cost.
Increased Overall Equipment Effectiveness
Predictive maintenance improves OEE by maximising availability, performance, and quality. Minimising downtime and optimising machine performance ensures operations run smoothly and efficiently.
Why implement predictive maintenance
Predictive maintenance is an investment, but the benefits far outweigh the costs. Monitoring key factors such as vibration and temperature allows businesses to build maintenance practices around real-time data rather than guesswork. By taking a proactive approach, organisations can improve equipment reliability, reduce costs, enhance workplace safety, and maximise overall equipment effectiveness.
For businesses looking to get started, entry-level, scalable systems provide an accessible solution. Systems like SKF Axios offer wireless, cloud-based monitoring of multiple machines and components, giving users instant visibility into equipment health. With easy setup, real-time data visualisation, and a flexible interface across multiple devices, SKF Axios makes predictive maintenance simpler and more effective.
Looking to implement predictive maintenance in your business? Our experts are here to help. Contact us today to find the right solution for your needs
ASIDE: OFFER – For a limited time, ACORN is offering FREE installation and setup training on the SKF Axios system when you purchase the five-sensor pack online.