What is Industry 4.0 and why is everyone talking about it?
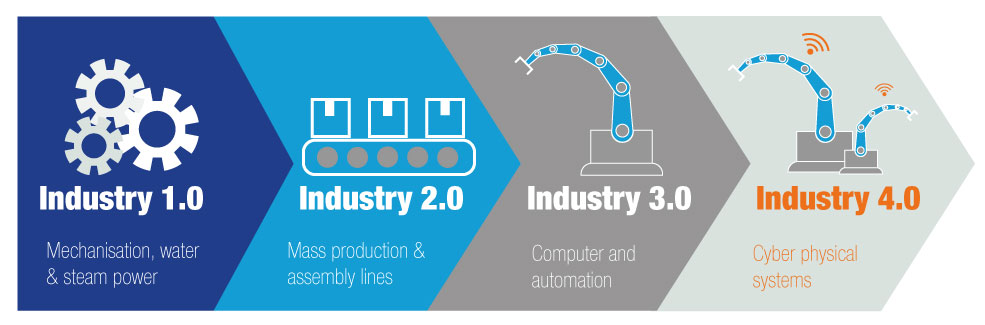
Industry 4.0: it seems to be the topic on everyone's lips. But, what does it actually mean? In an age supposedly on the cusp of a 4th industrial revolution, why do you need to move into 'Industry 4.0' and how can you make it as easy and pain free as possible?
As industry gears up towards this 'revolution', it’s important for your plant to move with it. Hydraulic and pneumatic systems are quickly becoming outdated, whereas their electrical counterparts can save space, costs and reduce the workload included in fitting, maintenance and replacing whilst also being better for the planet.
Be above the competition
Industry 4.0 in absolute basic terms is the move to turn our factories into 'smart factories'.
Machinery in smart factories uses artificial intelligence to make decisions on how to perform tasks at a greater speed and higher efficiency. Machines that use artificial intelligence are generally able to change and update how they work based on errors they encounter - essentially, they can problem solve without human intervention (this is only on a general scale - human intervention is still required during maintenance and repairs). This can aid in the full life cycle of production with reminders when maintenance or external inputs are required, meaning maintenance and downtime costs can be dramatically cut whilst also producing higher efficiency throughout the machining process.
The Internet of Things and Cloud computing
Whether it be on your desktop or via your smartphone, we are sure you will have heard of 'the Cloud'. The invisible area where all your information and content are stored, ready to be used at any time. Well, this is essentially what "cloud computing" is in Industry 4.0.
Cloud computing, as used in automated equipment, collates and stores data that can be easily accessed in cyber space. Where Artificial Intelligence (AI) can determine the optimum running of the equipment. You are also not then limited to the processing power of the machine and can process infinite amounts of data.
This development is the next step towards mobile devices that can access home appliance over the 'Internet of Things' – the next stage in the move towards Industry 4.0. This form of data storage and sharing allows machinery to communicate and interact over the internet, allowing users to remotely monitor and control devices.
Optimised maintenance
Smart factories keep maintenance and downtime to a minimum. The machines in a factory environment can connect to the cloud on a factory level or company level – this allows connections to be made between a company’s machinery in their factories all over the world. Real time data can be analysed to determine the best routine maintenance or overhauls when required. If connected to an ERP system, this can also re-route the workload to other machines or factories within the company.
Moving to Industry 4.0
The idea of moving your entire operation to Industry 4.0 in one fell swoop may seem daunting, unrealistic and just plain expensive. However, the move to automated equipment is already happening, and those who don’t move with it can be left behind. So, how do you take the hassle out? The Optimised Motion Series can help you to make an easy and vital step towards Industry 4.0. The OMS series can integrate into existing systems or be easily installed as an entire unit without the need to assemble individual parts. Not only this, but it is easy to configure systems via the web server, making it easier than ever to update your positioning systems.
Optimised Motion Series can make use of ‘cloud computing’, which is completely in line with Industry 4.0, making it an easy step towards the 4th industrial revolution. ACORN can design, quote and supply your next step in smart machinery. All you need is a contact number.
Get in touch today and talk to our dedicated Linear division about Electrical Automation and your next step into Industry 4.0.