What are the different bearing arrangements and where are they used?
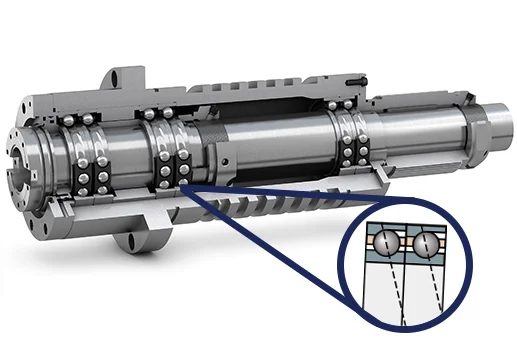
Bearings are critical components in many machines, providing rotational or linear motion while reducing friction and handling stress. Super precision bearings are essential for high-performance applications where accuracy, speed, and rigidity are paramount. Understanding the various bearing arrangements and their suitability for specific conditions is key to choosing the right solution with confidence and peace of mind.
It's important to remember that assessing the operating environment of your bearings is essential to understanding the different arrangements that are required for your machinery to work at its best.
Assessing the Operating Environment
Let’s look at how to assess your operating environment and application needs:
- Operating environment: Bearings might be exposed to contaminants such as dust, moisture, or chemicals. To prevent premature wear and failure, selecting a bearing arrangement that incorporates effective seals or lubrication is essential in such conditions.
- Maximum operating speed: Bearings must withstand the rotational speed demanded by the application. High-speed operations require bearings with low friction, precise geometry, and stable materials to maintain performance.
- Operating temperature: Applications involving significant heat or temperature fluctuations demand bearings designed for thermal stability. Improper handling of temperature variations can lead to wear or loss of precision.
- Rigidity requirements: For applications needing enhanced stiffness, such as in machining or robotics, specific bearing arrangements provide increased rigidity to minimise deflection and improve accuracy.
- Load combinations: Understanding the effect the applied load has on the bearing arrangement will help with the selection process and, crucially, will help define which arrangement is required in the correct orientation to the applied load.
Check out our range of precision bearings available to buy today
Types of Super Precision Bearing Arrangements
Super precision bearings can be configured in various arrangements to optimise performance for different operating and loading conditions, helping you find the perfect fit for your specific needs. Below are common arrangements and their typical applications:
Universal combination (DU – 2 row)
These bearings are designed to be mounted in pairs and are preloaded for high precision. Universal combinations offer flexibility for:
Back-to-back (DB)
Back-to-back (or DB) arrangements provide high rigidity and resistance to tilting moments and are commonly used in applications requiring stability under heavy radial and axial loads. These arrangements are often found in high-speed turbines and control systems.
Face-to-face (DF)
Face-to-face (or DF) arrangements accommodates slight misalignment better than DB, suitable for applications where space constraints necessitate a more compact design. Scanners and surgical tools often use DF configurations for compact design and alignment flexibility.
Tandem (DT)
Tandem (or DT) arrangements handle higher axial loads in one direction by distributing the load across two bearings. These arrangements are commonly found in aerospace applications such as high-speed turbines and control systems. They are also found in robotics due to the stiffness and load-handling capabilities.
Universal combination (DUD – 3 rows)
DBD
DBD arrangements improve handling of combined loads and moments, often used in live centres of spindles in precision grinding machines and other high-rigidity applications for rigidity and load management.
DFD
DFD arrangements offer better alignment flexibility than DBD while maintaining load capacity, often found in ball screw supports.
DTD
DTD 3 row arrangements provide even greater axial load capacity, particularly in one direction. They are suitable for application like high-speed turbines and axial compressors, they are also common in robotics due to the stiffness and load-handling capabilities.
Universal combination (QU – 4 rows)
DBB
A DBB arrangement ensures maximum rigidity and resistance to angular deflection, this makes it ideal for CNC machining centres where precision and stability are critical. CNC machining centres and grinders also utilise DBB arrangements for rigidity and load management.
DFF
Provide good axial and radial load capacity with some flexibility for misalignment.
DTT
Designed for extremely high axial loads in one direction, DTT arrangements are often found in axial compressors and turbines for their superior load capabilities and thermal stability.
DBT
DBT offer a balance of axial and radial load handling with flexibility for directional force distribution.
DFT
DFT blend alignments tolerance with enhanced axial load capacity and are often found in axial compressors and turbines for their superior load capabilities and thermal stability.
Choosing the Right Bearing Arrangement
Selecting the optimal bearing arrangement involves analysing load requirements, assessing environmental factors, and prioritising application goals. By understanding these factors, you can ensure the chosen super precision bearing arrangement meets the specific demands of your application, providing reliable performance and extending the bearing’s service life.
With the right choice, you’ll achieve lasting performance and peace of mind. Talk to our product experts for help selecting the best options for your machinery or order your arrangements from our website.