The Importance of Proper Bearing Lubrication for Optimal Performance
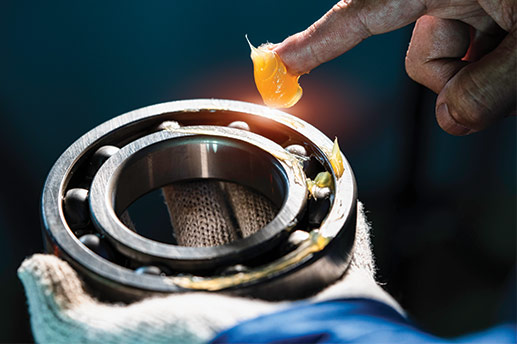
Bearings are the unsung heroes in most machinery. They allow for smooth rotation or linear movement, letting equipment run with minimal friction. However, without the right type and amount of lubricant, they’re vulnerable to excessive heat, contamination, and, ultimately, failure. Surprisingly, lubrication-related issues are a leading cause of bearing failure. A study from SKF found that they attribute 36% of premature bearing failures to poor lubrication practices.
Why Bearing Lubrication is Crucial
Bearings are essential components in machinery, allowing smooth rotational or linear movement while minimising friction. However, bearings are vulnerable to excessive heat, contamination, and even failure without the right type and amount of lubricant. With properly lubricated bearings, you’ll not only avoid frequent maintenance headaches but also extend the life of your machinery and minimise costly downtime.
Lubricants, such as oils and greases, serve two primary functions:
- Reducing friction: By forming a thin film between the moving parts, lubricants minimise metal-to-metal contact, reducing wear and heat.
- Protecting against contaminants: Lubricants can act as a barrier against dust, dirt, and other particles, helping to prevent these contaminants from getting into the bearing and causing damage.
Common Lubrication Mistakes That Cause Bearing Failure
Many lubrication issues can result in early bearing failure, often impacting production and repair costs. Here are three of the most common mistakes and how to avoid them:
- Insufficient Lubrication
Bearings need a specific level of lubrication to function correctly, so running them without enough lubricant or missing reapplications can cause bearings to eventually seize up. This is particularly damaging for machinery that requires consistent uptime, as inadequate lubrication leads to dangerous operating conditions due to increased friction, overheating, and breakdown.
- Over-lubrication
While it’s easy to assume more is better, over-lubrication can be just as harmful as under lubrication. When too much lubricant is applied, excess can leak through the bearing’s seal. This not only wastes valuable resources but also damages the seal; when this happens, contaminants like dirt or dust can make their way into the bearing, potentially leading to failure over time.
- Using the Incorrect Lubricant
Not all lubricants are created equal, so it’s essential to choose the right lubricant type for your machinery, as different environments require different lubrication solutions. Lubricants range from oils to greases, and each has unique properties designed to meet specific conditions. For example, a bearing used in a high-temperature environment, like an oven, needs a lubricant capable of withstanding extreme heat. Using an oil or grease not designed for the given temperature can lead to rapid breakdown of the lubricant, leaving the bearing exposed to damage.
Best Practices for Effective Bearing Lubrication
Here are some essential tips to help ensure optimal bearing lubrication and extend the life of your equipment:
- Choose the right lubricant: Assess your operating environment carefully before selecting a lubricant. Temperature, speed, and load requirements all play a role in determining the best choice between oils, greases, and high-temperature-resistant lubricants.
- Create a regular maintenance schedule: Consistent, scheduled maintenance prevents issues from building-up over time. Routine checks and re-lubrication help keep bearings functioning efficiently.
- Consult with a Lubrication Expert: Not every lubrication type or method is suited for all bearings, so working with a professional like our Lubrication Product Manager, Andrew Howard can be invaluable. Andrew can help you select the most effective lubrication and maintenance plan for your machinery, ensuring that lubrication is not only applied correctly but also maintained.
Conclusion
Proper bearing lubrication is more than a maintenance task; it’s a critical step in ensuring the optimal performance and longevity of your machinery. By avoiding common mistakes (such as under-lubrication, over-lubrication, and using the wrong lubricant type) you can reduce friction, minimise downtime, and enhance the overall reliability of your industrial equipment. ACORN’S Lubrication specialist can help you create an intuitive lubrication strategy to ensure that you’re not only protecting your bearings, but also your bottom-line.