The ACORN Bearing Compendium: How are bearings made, Part 3
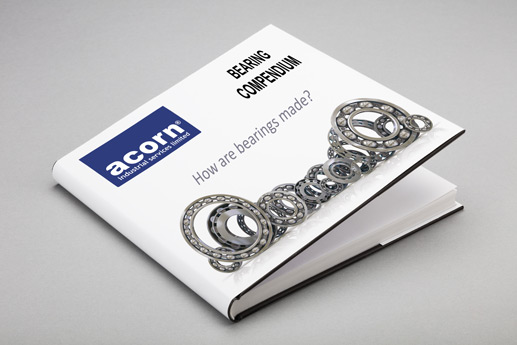
Bearings have been used for centuries to facilitate rotating motion, offering support to shafts whilst reducing friction. You will find bearings in almost every application, from cars and bicycles to washing machines and ovens, along with most industrial machinery.
There are many different types of rolling bearing, including ball bearings, roller bearings, needle bearings and tapered roller bearings, all offering their own range of features and benefits. These are available in an endless range of sizes to suit every possible application.
This article will explain how each component of a bearing is made and then assembled to form the bearings you see in machinery today.
What are bearings made from?
The most common material for bearings to be manufactured from is steel. The reason that most bearings are made of steel is due to its high levels of strength and good tolerance to stress – essential qualities for any bearing.
There are many other materials that may be used in bearings, including ceramic, bronze, cast-iron and plastics. However, steel remains the most common.
The industry standard classification for bearing steel is 52100. This means that the steel consists of alloys of one percent chromium and one percent carbon for added strength. The steel is then hardened through heat treatment. In applications which may be subject to corrosion, 440C stainless steel may be used.
Whilst many bearing cages are manufactured from thin steel thanks to its high level of rigidity and heat resistance, there are also many other options of materials when it comes to the bearing cage. These include plastic, fiberglass and bronze. Bronze is common in roller bearing cages thanks to its ability to dissipate heat away from the rolling elements, helping to extend bearing life.
Ultimately, the bearing material required will depend on the application it is being fitted to, along with the operating environment.
What is a bearing made up of?
Although some bearings may differ from the standard construction, most bearings consist of an inner and outer race, rolling elements and a cage or retainer.
The races of a bearing are simply metal rings which have a groove known as a raceway where the rolling elements rest. This raceway guides the rolling element around the bearing, preventing them from slipping out of the bearing during operation. The largest ring is known as the outer race and the smallest ring, in which the shaft rides, is known as the inner race.
The rolling elements of a bearing are situated between the bearing’s inner and outer rings and are used to transmit rotational motion whilst minimising the coefficient of friction.
There are many different types of rolling element available, each with different properties and benefits. The type of rolling element that you’ll choose will depend on your application requirements including load, speed and operating conditions.
Rolling elements are divided into balls and rollers. Generally speaking, ball bearings are typically used for high-speed applications with low to moderate load requirements, whilst roller bearings are preferred for applications with heavy load requirements operating at moderate speeds. However, there are many variations of each type of bearing, with options available to suit every application requirement.
The cage of the bearing, also known as the retainer, is responsible for holding the rolling elements of the bearing in place, maintaining radial spacing whilst preventing them from falling out of the bearing.
The races, rolling elements and cage are often combined with a sealing solution during assembly to protect the bearing and help to retain lubricant.
How are bearing races manufactured?
Most bearings consist of an inner and an outer race. These metal rings begin as a piece of steel tubing which is cut to a size slightly larger than the required dimensions using a machine similar to a lathe. The reason that the race is initially cut larger than required is to allow for shrinkage during heat treatment.
After the race is cut, it is then put into a heat-treating furnace of up to 850oC for several hours. The race is then removed and dipped quickly into an oil bath to cool and harden. However, this process can make the races brittle, so they are then tempered using an oven of around 150oC. The races are then left to cool in the air, where they reach their maximum level of strength and rigidity.
Once the race has been through the heat treatment process, it is ready for finishing. This is done using grinding wheels, giving the bearing its final smooth surface. The bearing races are then ready for assembly.
How are the rolling elements of bearings made?
There are many different types of rolling element that can be found within a bearing. These include balls, cylindrical rollers, tapered rollers, needle rollers and spherical rollers. The manufacturing process is similar for each but in this article, we’ll focus on how balls are made.
Despite the simple shape of a ball, they have a complex manufacturing process. They begin life as a thick piece of steel wire which is fed into a cold heading machine. Within the machine, it is cut to length and then pressed. This process is known as cold heading as no heat is applied during the process, which is most commonly used when manufacturing the heads for bolts and screws.
The ball is then left with a bulge around the centre, known as the flash. To remove this flash, the balls are put into rough grooves, between the faces of two cast iron discs. One disc rotates as the other remains stationary. As the disc rotates, the ball moves in its groove, with the friction removing the flash to leave a smooth surface.
After the flash has been removed, the balls are then ready to be heat treated in the same way as the races to optimise their strength and durability. Like the races, the balls will be slightly bigger than their required size to allow for shrinkage during this heat treatment process.
Once the balls have been heat treated, they are ground into a perfect spherical shape, within a few ten thousandths of an inch of their specified size. They are then moved to a lapping machine where cast iron wheels use an abrasive lapping compound to finish the balls. This can take up to ten hours, depending on the required levels of precision.
The process of manufacturing balls for ball bearings is complex but results in high quality rolling elements which have outstanding levels of strength with minimal friction.
How are bearing cages manufactured?
The two most common materials for bearing cages are steel and plastic. The process for manufacturing each of these is different, so we’ll discuss both methods.
Steel bearing cages begin life as a thin sheet of metal. The cage is stamped from the material in the same way you’d cut cookies. After this, the cage is put into a die where it is bent to its final shape. The die is like a mould, shaping the cage into its desired form. When the cage is taken from the die, it is complete and ready for assembly.
On the other hand, plastic bearing cages are typically constructed using a method known as injection moulding. Melted plastic is inserted into a metal mould and left to harden into the shape of the bearing cage. The mould is then opened and the completed cage removed ready for assembly.
How are bearings assembled?
When all parts have completed the manufacturing process, the bearing is ready for assembly. First of all, the races are fitted together and the rolling elements inserted and spaced evenly around the bearing. The cage is then fitted to hold the rolling elements in place. Plastic cages generally snap together whilst steel cages need to be riveted.
Once the bearing is assembled, it may be coated to prevent rust. Grease or lubricant may be inserted into the bearing and seals fitted depending on the type of bearing. The bearing will then be packaged carefully ready for distribution.
How is bearing quality assessed?
The quality of a bearing is essential for precise and reliable operation, so every bearing goes through a strict quality control process.
Before being used in the manufacturing process, steel is tested to ensure that it contains the correct quantity of alloy metals. This ensures that the bearing will be of the highest quality before it is even created.
Throughout the heat treatment process, the parts will be tested for hardness and toughness to ensure that they meet the quality standards. Shapes and sizes of each component are also regularly assessed throughout the production process. This includes ensuring that the surfaces of the rolling elements are exceptionally smooth to minimise friction, and that they are perfectly round in shape.
Bearings are manufactured to strict tolerances. This is the margin of error that is acceptable when it comes to dimensions and is measured by the ABEC rating system. ABEC 1 bearings have moderate levels of precision whilst ABEC 9 bearings are exceptionally precise. The quality control process will ensure that the bearings are manufactured to the specified tolerances.
To sum up
Bearings are highly precise machine components which must be carefully manufactured to strict tolerances. The bearing manufacturing process will vary depending on the type, material and brand of the bearing but we have given you an overview of the typical manufacturing method of the most common bearings.