Proactive vs preventative maintenance: What is right for your machinery?
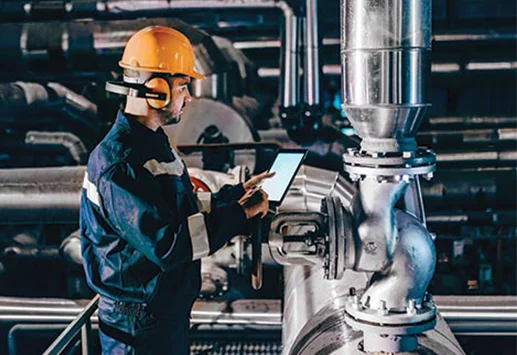
Maintaining machinery effectively is crucial for maximising efficiency, minimising downtime, and controlling costs. Businesses face an essential decision when it comes to maintenance strategies: should they opt for proactive maintenance, which relies on advanced data analysis, or preventative maintenance, which follows a pre-scheduled routine? Each approach offers unique benefits and challenges, and choosing the right strategy depends on the nature of your machinery and operational priorities.
What is Proactive Maintenance?
Proactive maintenance (also known as Condition Monitoring) is a forward-thinking approach that uses real-time data and analytics to predict and address potential issues before they occur. With systems such as SKF Axios, sensors are installed on machinery, and performance metrics such as vibration and temperature are continuously monitored. These insights enable maintenance teams to identify anomalies and address root causes proactively.
Advantages of Proactive Maintenance:
- Minimised Downtime: If critical machinery fails, it often leads to costly disruptions. Proactive maintenance reduces unplanned downtime by addressing issues early.
- Root Cause Resolution: This approach prevents recurring issues by focusing on the underlying causes of potential problems.
- Optimal Equipment Lifespan: Real-time data helps you maintain machinery at peak performance, extending its usable life.
Drawbacks of Proactive Maintenance
While effective, proactive maintenance comes with challenges such as high initial costs for sensors and analytics, complexity in implementation, and the need for specialised personnel to manage the system. Continuous monitoring can be resource-intensive, and for non-critical equipment, the investment may not justify the benefits.
When to Use Proactive Maintenance:
This method best suits critical machinery or operations where downtime would result in significant financial losses or safety risks. While it requires investment in sensors and data analysis systems, the cost savings from avoided failures can make it highly economical in the long run.
What is Preventative Maintenance?
Preventative maintenance follows a pre-determined schedule based on time, usage, or manufacturer recommendations. For example, a machine might undergo servicing every three months or after 500 hours of use, regardless of its current condition.
Advantages of Preventative Maintenance:
- Simplicity: Scheduled routines are easy to implement and don’t require advanced technology or constant monitoring.
- Lower Initial Costs: Compared to the setup and tools needed for proactive maintenance, preventative maintenance is generally less expensive upfront.
- Consistency: Regular inspections help to identify and address wear and tear before it leads to failure.
Drawbacks of Preventative Maintenance:
While it is cost-effective for non-critical equipment, this approach can lead to unnecessary part replacements or overlook unforeseen failures. Over time, these incremental costs can add up, especially if the maintenance is overly conservative.
When to Use Preventative Maintenance:
Preventative maintenance is ideal for less critical machinery where the costs of downtime are manageable. It’s also suitable for organisations that want to establish a predictable maintenance budget.
How to Decide What’s Right for You
- Evaluate Criticality of Equipment:
Proactive maintenance is often the best choice for machines where failures lead to substantial costs or safety hazards. For less vital equipment, preventative maintenance can suffice. - Assess Your Budget:
Proactive maintenance demands investment in monitoring technology and skilled personnel to interpret data. Preventative maintenance, on the other hand, may fit smaller budgets better. - Consider Operational Complexity:
Complex operations often benefit from the precision of proactive maintenance. Simpler systems may not justify the cost of advanced data analytics. - Analyse Long-Term Costs:
While preventative maintenance might seem cost-effective initially, it can result in higher cumulative costs over time. Conversely, proactive maintenance can provide substantial savings by avoiding expensive repairs and downtime.
Check out the SKF Axios page here
Conclusion
Both proactive and preventative maintenance have valuable roles in machine maintenance. The right choice depends on the criticality of your equipment, your budget, and your long-term operational goals. Adopting a hybrid strategy using proactive maintenance for critical machinery and preventative maintenance for less vital assets can offer the best of both worlds. By aligning your maintenance approach with your business needs, you can ensure maximum efficiency, reliability, and cost-effectiveness.