Preventing Bearing Failure: Best Practices and Maintenance Tips
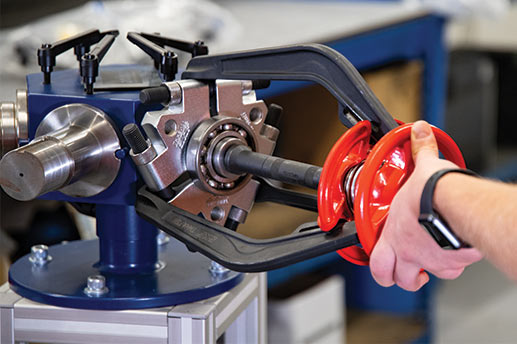
Proper maintenance is key to maximising bearing life and equipment uptime. A bearing’s expected lifespan depends not only on its quality but also on the care taken during installation, maintenance, and dismounting. Leading bearing manufacturer SKF developed the concept of the bearing life cycle, highlighting maintenance practices that help prevent premature bearing failure at each stage of use.
In this guide, we’ll explore these practices to help you keep your bearings and equipment running smoothly.
Buy a bearing
Ensuring that the bearing you select is correct for your application is essential for bearing failure prevention. When selecting a bearing, make sure to assess environmental factors and operational demands, including:
- Load ratings
- Operating speed
- Operating conditions (eg, heavy-duty applications)
- Temperature
- Environmental considerations (eg, corrosive or dirty conditions)
- Lubrication needs
Considering these aspects will give your bearing its best chance at an optimum service life. For example, selecting a sealed stainless steel ball bearing for an application working in a food processing plant will last longer under intense wash-down conditions than standard bearings. When selecting a bearing, if you’re unsure of what your machinery requires, you can talk to our Bearing Expert, who will help to determine what is best.
Mounting
It may not seem like it, but 16% of all premature bearing failures can be attributed to incorrect mounting. To ensure you’re giving your components their best chance of reaching their service life, it’s essential to use the correct tools for the job. Whether your bearings require force, heat or hydraulics, consider the following mounting techniques:
- Cold mounting
Traditionally, cold mounting involved using a hammer, which risks misalignment. A fitting tool like the SKF TMFT 36 applies force equally to the bearing ring, helping to prevent damage.
- Heat mounting
Heating can be dangerous when done incorrectly, and using naked flames poses a health and safety nightmare for workers. Using an induction heater is a much safer technique as users can control temperatures with the appropriate equipment.
- Hydraulic mounting
Using an oil bath to heat bearings is not only a massive risk to safety but can also contaminate bearings, leaving them vulnerable to premature failure. Instead, simply swap the oil for a hydraulic fitting kit, which can work using an oil injection method or a drive-up method.
Lubrication
Ensuring that you’re selecting the correct lubricants for the running environment helps to prevent 50% of premature failures due to poor lubrication or contamination.
Adhering to the best practices for effective lubrication will give your bearings the best shot at reaching their service life potential. By choosing the correct lubrication based on your application's running temperature, speed, and load requirements, and creating a regular maintenance schedule, you’ll give your bearings their best possible chance.
Talking to a Lubrication expert like Andrew Howard about your lubrication requirements can significantly improve machinery uptime and reliability.
Alignment
Misaligned shafts can wreak havoc on machinery, often resulting in increased vibration, directly leading to premature bearing failure. Using tools like the TKSA series can prevent these issues. Proper alignment protects bearings and other components, helping your equipment run smoothly.
Condition Monitoring
Being able to see the condition of bearings continuously helps ensure a long bearing service life, eliminating unplanned downtime and reactive maintenance. With a reduction in reactive maintenance comes a reduction in maintenance costs.
There is a wide range of condition-monitoring solutions on the market, ranging from basic inspection equipment to advanced-level systems. If you’re looking for a continuous monitoring system, it is advised to start with simple-to-use, ‘plug & play’ systems that are scalable and can be integrated with other systems. One such system is the SKF Axios, which uses a web-based cloud system to gather data via magnetic sensors on machinery. When anomalies are reported, users can then take a reading using inspection equipment and carry out maintenance as required.
Check out the SKF Axios page here
Dismounting
Surely, dismounting a bearing can’t have that much impact on service life and worker safety. That's where you’d be wrong! If dismounted incorrectly, not only can this impact the shaft and cause damage to the surrounding equipment, but it also puts workers' health & safety at risk.
Similar to mounting a bearing, you can dismount using mechanical, heat, or hydraulic methods. The most used method is with a bearing puller, which offers a quick and easy dismount for a range of bearing sizes and housing methods. There are also options for hydraulic-assisted bearing pullers, which are suitable for large bearings.
Conclusion
Effective bearing maintenance, from selection and mounting to condition monitoring and dismounting, can significantly enhance bearing life and reduce downtime. By following these best practices, you’ll extend the lifespan of your bearings and improve the reliability of your equipment. Alternatively, you can talk to our Bearing & Maintenance Expert, Andy Fletcher, who can help you to create a comprehensive maintenance strategy to save your business's bottom line.