How to get the most out of your roller chain
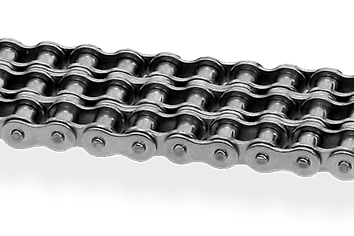
Roller chain is found in a vast assortment of applications across every industry, where it is used both to transmit power and to convey material. As so many applications are dependent on roller chain, it is vital that service life is optimised to prevent unnecessary downtime and costs to the business.
Every roller chain has an expected service life, according to the specification of the chain and the conditions of usage. Even the highest quality of chain which is used exactly as the manufacturer specifies will slowly wear.
Premature failure occurs when the wrong chain is specified for the application, or when manufacturer instructions for use are not followed. In this article, we will explain how to get the most out of your roller chain, reducing premature failure and optimising service life.
One of the most common causes of excessive roller chain wear is incorrect or insufficient lubrication. Ensuring that the correct type and quantity of lubrication is applied at the correct intervals will give your roller chain the best possible chance of achieving its maximum possible service life.
The type of lubricant needs to be carefully selected based on the drive’s specifications and the operating environment. The optimum lubrication will help to reduce wear within the chain, as well as cushioning impact loads and helping to dissipate heat.
Installing an automatic lubrication system can ensure that the right quantity of lubricant is applied at the right interval, reducing manual effort and removing the opportunity for human error. At ACORN, we have a wide variety of automatic lubrication systems available from world-class manufacturers such as SKF, with options to suit every application and industry.
Roller chain often operates in environments where contamination is commonplace. Abrasive contaminants such as dirt and dust can cause damage to the internal mechanisms of the chain, accelerating wear. Contamination by dirt, rusting or exposure to corrosive environments may prevent lubricant from penetrating pins.
It is important to keep the operating environment as clean as possible to avoid the chances of contamination entering the roller chain. If exposure to contamination is inevitable, select a roller chain which is designed for the environment. For example, Tsubaki’s Neptune chain has been specifically designed with corrosive environments and extreme temperatures in mind.
Ensuring the alignment of both shafts and sprockets can help to extend the service life of roller chain. Misalignment can cause uneven loading across the chain width, leading to wear on roller linkplates and sprocket teeth. You can ensure that both sprockets and shafts are aligned and help to reduce premature chain wear with the help of a simple straight edge, or a more sophisticated and accurate laser alignment tool such as those available from SKF.
Ensuring that the correct roller chain is selected for the application requirements is critical, in order to give your chain the best possible chance of achieving its maximum service life. Excessive loads are a common cause of premature chain wear. Care must be taken to ensure that the right chain product is selected for the predicted application load, and this should be reassessed at regular intervals to ensure that loads experienced during operating do not exceed the manufacturer’s specifications for the product.
ACORN supplies a vast range of roller chain from world-class manufacturers such as Tsubaki, Renold, IWIS and SKF. Couple this with our industry-leading experts who are on hand to assist you at every stage, and there’s no doubt that ACORN is the supplier to turn to for all of your power transmission requirements. What if you need a specific legth of chain? ACORN can cut your Tsubaki chain to your required length so you can order exactly what you need with no wasteage.
Contact your local knowledgeable sales team today for more information on how you can get the most out of your roller chain, maximising service life and reducing unplanned downtime.