How To Get The Most Out Of Your Bearings
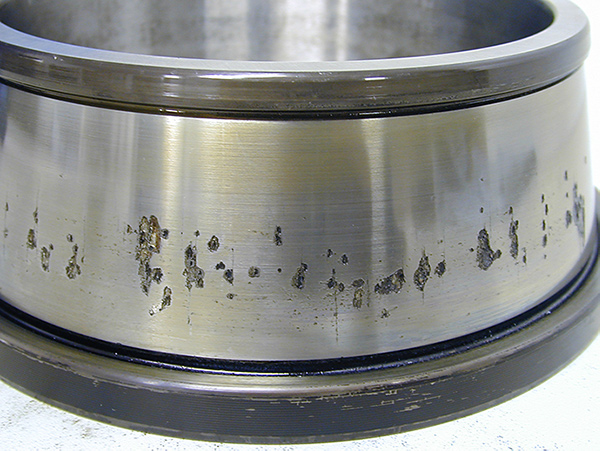
Conveying motion whilst reducing friction between moving parts, there is no denying that bearings are under a lot of stress. This stress causes wear over time, which will eventually cause the bearing to fail. It is essential to have a comprehensive maintenance plan in place in order to avoid bearings failing prematurely, and to reduce both costs and downtime for the business.
Bearing Mounting Practices
With 16% of premature bearing failures attributed to poor fitting practices, it has never been more critical to ensure that you are following an appropriate process for mounting and dismounting your bearings.
Tools such as bearing heaters, bearing fitting toolkits and bearing pullers are all safe and effective methods of fitting and removing bearings, which reduce the risk of bearing damage. It is also essential to ensure that staff who are responsible for changing bearings continuously update their training to ensure that they are aware of changing practices and up to date advice on the mounting and dismounting of bearings.
Bearing Selection
If a bearing has failed prematurely then it is likely to be due to incorrect bearing selection. Whilst this could be because the bearing is at the end of its lifecycle, 34% of bearing failures can be attributed to fatigue.
The bearing chosen needs to be suitable for the speed and load of the application, as well as the environmental conditions that it will be subjected to such as high temperatures, electric currents or frequent washdowns.
External Contamination
External contamination such as dust, debris and water can significantly impact the lifespan of your bearing if not managed successfully. An effective sealing solution which is suitable for the environmental conditions needs to be used.
All too commonly, a high-quality bearing is purchased but then paired with a sub-standard seal. It is essential to pair your bearing with the right protection, according to the bearing, application and environmental conditions.
If the bearing is heated for fitting, it is important to consider how this may impact the seal, as some seals may degrade at high temperatures and become less effective. If using an induction heater, 110⁰c should be more than ample to achieve this, without harming the bearing.
Predictive Maintenance
Another way to increase your bearing life is through condition monitoring of your machine health. Condition monitoring can proactively detect misalignment, excess vibration, lubrication issues and temperature changes, which could indicate an issue that may cause your bearings to fail prematurely.
Continuous monitoring of the condition of your machine health may alert you to an issue early enough that you can correct it before it causes your bearing to fail.
Moreover, with workers 28% more likely to have an accident performing reactive maintenance over proactive, you can improve your worker’s safety at the same time.
Lubrication
Problems with lubrication account for around a third of premature bearing failures. This could be too much, too little or the wrong type of lubrication.
Firstly, it is essential to ensure that the correct type of lubrication is used to suit the application conditions: the speed, load and temperature of the application must be taken into consideration.
It is also worth considering an automatic lubrication system. As bearings are often amongst the most inaccessible components of an application, the required re-lubrication intervals are commonly not met, causing bearings to wear prematurely. An automatic lubrication system takes the manual effort out of lubrication, ensuring that the correct amount is applied, at the correct interval.
Bearings are crucial components of any application, and it is important to look after them in order to give them the best chance of achieving their maximum service life.
For more information on how you can get the most out of your bearings, contact your local branch today.
Don't miss out, subscribe to our emails and get the latest Tips, How-To's, Special Offers, and Industry & Company News!