How to choose the right coupling for your mixer
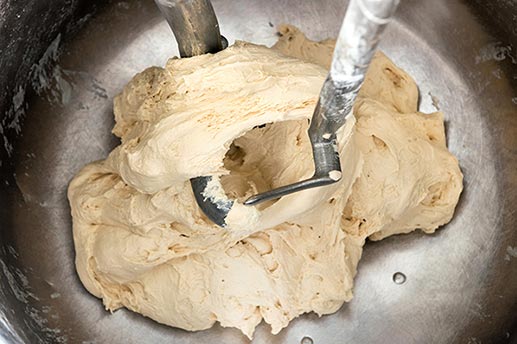
The mining and quarrying industry brings harsh conditions at a fast pace, putting components to the test. Mixers are common in the industry, consisting of an electric motor coupled to a paddle or impellor. But the choice of coupling that connects the motor with the paddle or impellor is critical to the successful operation of the mixer.
It is important to note that while the motor is supported by a bearing, the paddle or impellor is not, making a rigid coupling the only option. There are three types of rigid coupling: set-screw, clamp-screw and flanged. Each of these couplings has its pros and cons, and which type of rigid coupling is selected will depend on the application requirements.
Set-screw rigid couplings
Set-screw rigid couplings are the most common type of rigid coupling in mixers and are suitable for use in a wide range of mixers. They are manufactured from a solid piece of material, with set-screws for fixing the coupling in situ.
The holding power of a set screw rigid coupling comes from the screw being tightened into the shaft, which must be manufactured from a softer material than the screws. The amount of torque able to be transmitted depends on the difference between the hardness of the materials.
The key disadvantage of using set screw rigid couplings in your mixer applications is that they cause the shaft to mar, making removal difficult. This means that set screw rigid couplings are not ideal in applications which require frequent paddle or impellor changes.
Clamp-style rigid couplings
Clamp-style rigid couplings wrap around the shaft evenly using compressive forces. This provides a secure fit without marring the shaft. These couplings are easily adjustable and can be removed and replaced infinitely without causing damage.
One-piece and two-piece variations are available, with the two-piece option allowing for servicing in-situ, without any removal of surrounding equipment required. This helps to reduce downtime whilst limiting damage to the impellor or paddle shaft.
The biggest disadvantage of a clamp-style rigid coupling is the cross-cut, which is the point of weakness in the coupling. This can cause the coupling to fail over time, although this is a rare occurrence.
Flange-type rigid couplings
Flange-type couplings are the least common type of rigid coupling for use in mixers. They have all the benefits of set-screw rigid couplings but they consist of two independent hubs which are connected using bolts. Each hub also has one or two set screws to hold the shaft in place.
Flange-type rigid couplings are mainly used where the benefits of set-screw rigid couplings are required but space is limited or the shaft is larger than 50mm in diameter.
The key disadvantage of flange-type rigid couplings is the assembly time required, as all bolts need to be removed for disassembly.
Ruland manufactures a wide range of set-screw, clamp-style and flange-type rigid couplings which are suitable for mixers, with materials such as zinc-plated steel, black oxide steel, 303 and 316 stainless steel available. All Ruland couplings are manufactured to strict quality standards and are RoHS3 and REACH compliant.
To ensure that the correct coupling is specified, technical specifications such as the speed and load of the application and the environment in which the mixer will be operating need to be closely examined. Luckily, our dedicated couplings centre is on hand to offer assistance. Contact our experts today to discover the optimum coupling for your mixer application.