Five steps to effective lubrication
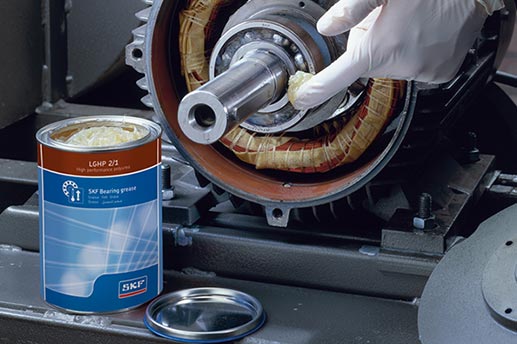
It’s easy to underestimate the importance of appropriate lubrication. However, with 36% of premature bearing failures as a result of inadequate lubrication, even the most sophisticated application manufactured using the highest quality components will be prone to premature failure without optimum lubrication.
Andrew Howard, our Lubrication Product Manager, has put together his top five steps to effective lubrication, to help you to reduce your risk of premature bearing failure due to lubrication issues.
For help creating the right maintenance schedule for your application, talk to Andrew
1. Initial selection of lubricant
The first step to effective lubrication is ensuring that the correct type of lubricant for the operating conditions and the environment has been chosen. Types of lubricant include oils to greases, with options such as low or high temperature, water resistance, high pressure, high load and high speed lubricants, to suit every application.
Seek expert advice if you’re unsure about which lubricant is most suitable for your application.
2. Storage of lubricant
Lubricant should always be stored in a cool, dry location. It should be clearly labelled and effectively sealed to avoid contamination which could degrade the lubricant during storage and later cause the bearing to fail prematurely once applied.
The recommended maximum storage period for greases is 2 years, and for lubricating oils is 10 years. However, this relies on reasonable stock keeping practices and protection from extreme temperatures.
3. Lubricant application
Always follow manufacturer instructions when it comes to the quantity of lubricant required, and the intervals for application. Too much lubricant can cause the seal to fail, allowing contamination to enter the bearing, whilst too little lubricant increases friction, raising the internal temperature of the bearing and causing wear.
Automatic lubricators are particularly useful for lubricant application as they ensure that the correct dose is applied at the correct interval, removing the opportunity for manual error.
4. Condition monitoring
Condition monitoring offers an insight into the condition of machine components. Raised internal temperatures could indicate a lack of lubrication within a bearing, causing excess friction. This early indication allows lubrication levels to be corrected, preventing premature failure of the bearing due to wear.
5. Re-evaluation of lubricant
Lubrication should be re-evaluated whenever there is a change in the operating conditions of the application. This will ensure that the type and quantity of lubricant is still appropriate for the application, helping to prevent lubricant degradation and prolong the life of machinery.
For advice on choosing the right lubrication for your machinery, contact your local sales team today.
You may also be interested in:
Taking the contamination out of lubrication: Effective lubrication for the food & beverage industry
How can condition monitoring reduce downtime in the mining and quarrying industry?