6 Reasons to Implement a Predictive Maintenance Plan
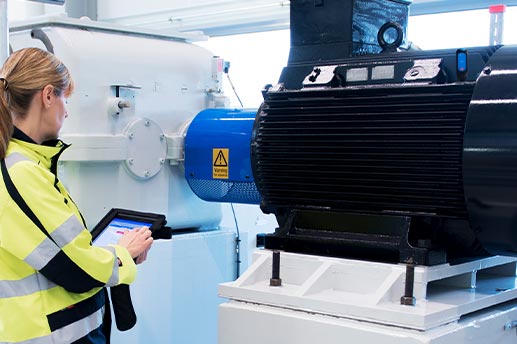
In manufacturing and industrial operations, maintenance keeps things moving. Traditionally, this has meant reacting when something breaks or carrying out routine servicing based on time schedules. But now, thanks to advances in technology, there's a more effective option. Predictive maintenance is changing the game by helping businesses stay one step ahead.
Key Takeaways
- Predictive maintenance is a proactive approach that uses real-time data to monitor machine health and identify issues before they lead to breakdowns.
- It increases equipment reliability, reduces downtime, and extends the lifespan of machinery.
- Businesses benefit from significant cost savings by avoiding emergency repairs and reducing unnecessary maintenance tasks.
- Predictive maintenance improves workplace safety by identifying risks early and supporting regulatory compliance.
- It supports sustainability goals by reducing energy use, waste, and the environmental impact of industrial maintenance.
- Using data-driven insights, teams can make smarter, more efficient maintenance decisions.
- Predictive maintenance contributes directly to improved Overall Equipment Effectiveness (OEE), boosting operational performance and output
What is Predictive Maintenance?
Predictive maintenance uses real-time data, such as temperature and vibration, to monitor machine health and spot issues before they turn into problems. This means fewer breakdowns, better repair timing, and longer-lasting equipment.
Why Predictive Maintenance is Important
1. Increased Equipment Reliability
One of the key advantages of predictive maintenance is the improvement it brings to equipment reliability. Instead of waiting for something to go wrong, predictive maintenance uses real-time monitoring and analysis to spot small changes that signal future issues. This gives your maintenance teams the time and information they need to step in early. The result is fewer breakdowns, more consistent machine performance, and a longer life for your equipment. All of this helps to keep operations running smoothly and efficiently.
2. Cost Savings and Improved Efficiency
Predictive maintenance helps prevent costly failures and reduces the need for emergency repairs. By only carrying out maintenance when it’s actually needed, you save time, money, and effort. You also avoid over-servicing, which means your team can focus their time where it really matters. Spare parts and resources can be managed more effectively too, which helps to lower inventory costs. Altogether, this approach supports a leaner, more efficient way of working, with benefits that feed directly into your bottom line.
3. Improved Safety and Compliance
In many industrial settings, equipment failure isn’t just inconvenient; it can also be dangerous. Predictive maintenance helps to minimise risk by identifying problems before they become safety concerns. Well-maintained machines are safer for your team and more likely to meet the strict requirements of safety regulations. This not only protects your people but also reduces the risk of costly legal issues and reputational damage. It shows that your business takes responsibility seriously.
4. Contribution to a sustainable workplace
Sustainability matters. Predictive maintenance supports your environmental goals by helping equipment run more efficiently and reducing unnecessary waste. When machines are serviced at the right time, they use less energy, operate more effectively, and last longer. Fewer part replacements mean less material waste and fewer breakdowns, which reduce the need for emergency interventions that can have a higher environmental cost. It’s a smart way to reduce your impact while staying productive.
5. Data-Driven Decision Making
Predictive maintenance is powered by data. Sensors and smart systems continuously collect information on how your machines are performing. This gives you a clear picture of what’s working, what needs attention, and when action is required. With this insight, your maintenance planning becomes more targeted and efficient. You can prioritise tasks, allocate resources wisely, and avoid unnecessary costs. Most importantly, you can make decisions with confidence, knowing they’re backed by accurate data.
6. Improved Overall Equipment Effectiveness (OEE)
OEE is a key metric used to measure the productivity of equipment, taking into account availability, performance, and quality. Predictive maintenance has a direct and positive effect on all three. Reducing downtime, identifying performance issues, and ensuring that machines are running at their best, helps to raise your OEE score. This leads to better output, improved product quality, and a more reliable operation overall.
Check out our maintenance equipment range here
Conclusion
Investing in a predictive maintenance strategy is a smart, forward-thinking investment. It gives you better control over your equipment, helps prevent problems before they happen, and supports a safer, more sustainable workplace. As technology continues to evolve, this approach is becoming an essential part of staying competitive.
At ACORN®, we’re proud to be certified Maintenance Partners and Authorised Distributors of SKF products. This reflects our commitment to helping customers like you find long-lasting, dependable maintenance solutions.
Want to learn more about how predictive maintenance could support your business? Speak to one of our Bearing & Maintenance Experts today.